Avec le développement de la science et de la technologie modernes, de plus en plus de matériaux techniques à haute dureté sont utilisés, tandis que la technologie de tournage traditionnelle n'est pas compétente ou ne peut pas du tout réaliser le traitement de certains matériaux à haute dureté.Le carbure revêtu, la céramique, le PCBN et d'autres matériaux d'outils ultra-durs ont une dureté, une résistance à l'usure et une stabilité thermochimique élevées à haute température, qui constituent la condition préalable la plus fondamentale pour la coupe de matériaux de haute dureté et ont obtenu des avantages significatifs en production.Le matériau utilisé par l'outil extra-dur, sa structure d'outil et ses paramètres géométriques sont les éléments de base pour réaliser un tournage dur.Par conséquent, la manière de sélectionner le matériau de l'outil ultra-dur et de concevoir une structure d'outil et des paramètres géométriques raisonnables est cruciale pour obtenir un tournage dur stable !
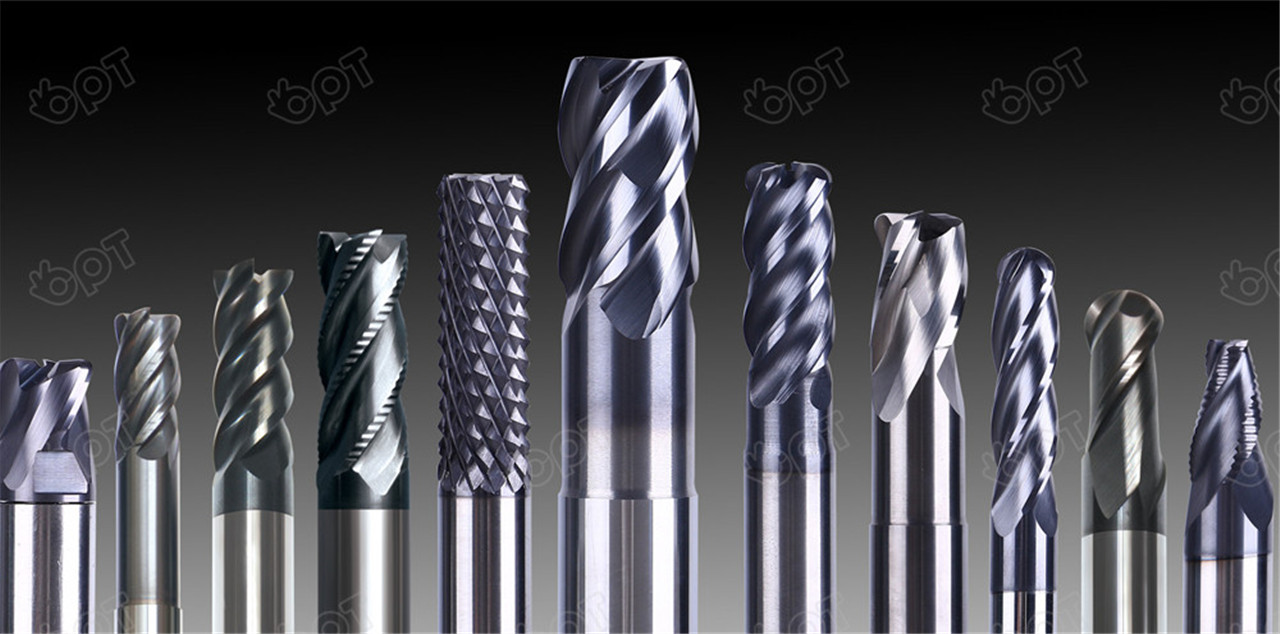
(1) Carbure cémenté revêtu
Appliquez une ou plusieurs couches de TiN, TiCN, TiAlN et Al3O2 avec une bonne résistance à l'usure sur des outils en carbure cémenté avec une bonne ténacité, et l'épaisseur du revêtement est de 2 à 18 μm.Le revêtement a généralement une conductivité thermique beaucoup plus faible que celle du substrat de l'outil et du matériau de la pièce à usiner, ce qui affaiblit l'effet thermique du substrat de l'outil ;D'un autre côté, il peut améliorer efficacement la friction et l'adhérence dans le processus de coupe et réduire la génération de chaleur de coupe.
Bien que le revêtement PVD présente de nombreux avantages, certains revêtements tels que l'Al2O3 et le diamant ont tendance à adopter la technologie de revêtement CVD.Al2O3 est une sorte de revêtement avec une forte résistance à la chaleur et à l'oxydation, qui peut séparer la chaleur générée par la coupe de l'outil spécifique.La technologie de revêtement CVD peut également intégrer les avantages de divers revêtements pour obtenir le meilleur effet de coupe et répondre aux besoins de coupe.
Par rapport aux outils en carbure cémenté, les outils en carbure cémenté revêtus ont considérablement amélioré leur résistance, leur dureté et leur résistance à l'usure.Lors du tournage de la pièce avec une dureté de HRC45 ~ 55, le carbure cémenté revêtu à faible coût peut réaliser un tournage à grande vitesse.Ces dernières années, certains fabricants ont amélioré les performances des outils revêtus en améliorant les matériaux de revêtement et d'autres méthodes.Par exemple, certains fabricants aux États-Unis et au Japon utilisent un matériau de revêtement AlTiN suisse et une nouvelle technologie de revêtement brevetée pour produire des lames revêtues d'une dureté aussi élevée que HV4500~4900, qui peuvent couper l'acier HRC47~58 à une vitesse de 498,56 m/min. .Lorsque la température de tournage atteint 1 500 ~ 1 600 ° C, la dureté ne diminue toujours pas et ne s'oxyde pas.La durée de vie de la lame est quatre fois supérieure à celle de la lame à revêtement général, alors que le coût n'est que de 30 % et que l'adhérence est bonne.
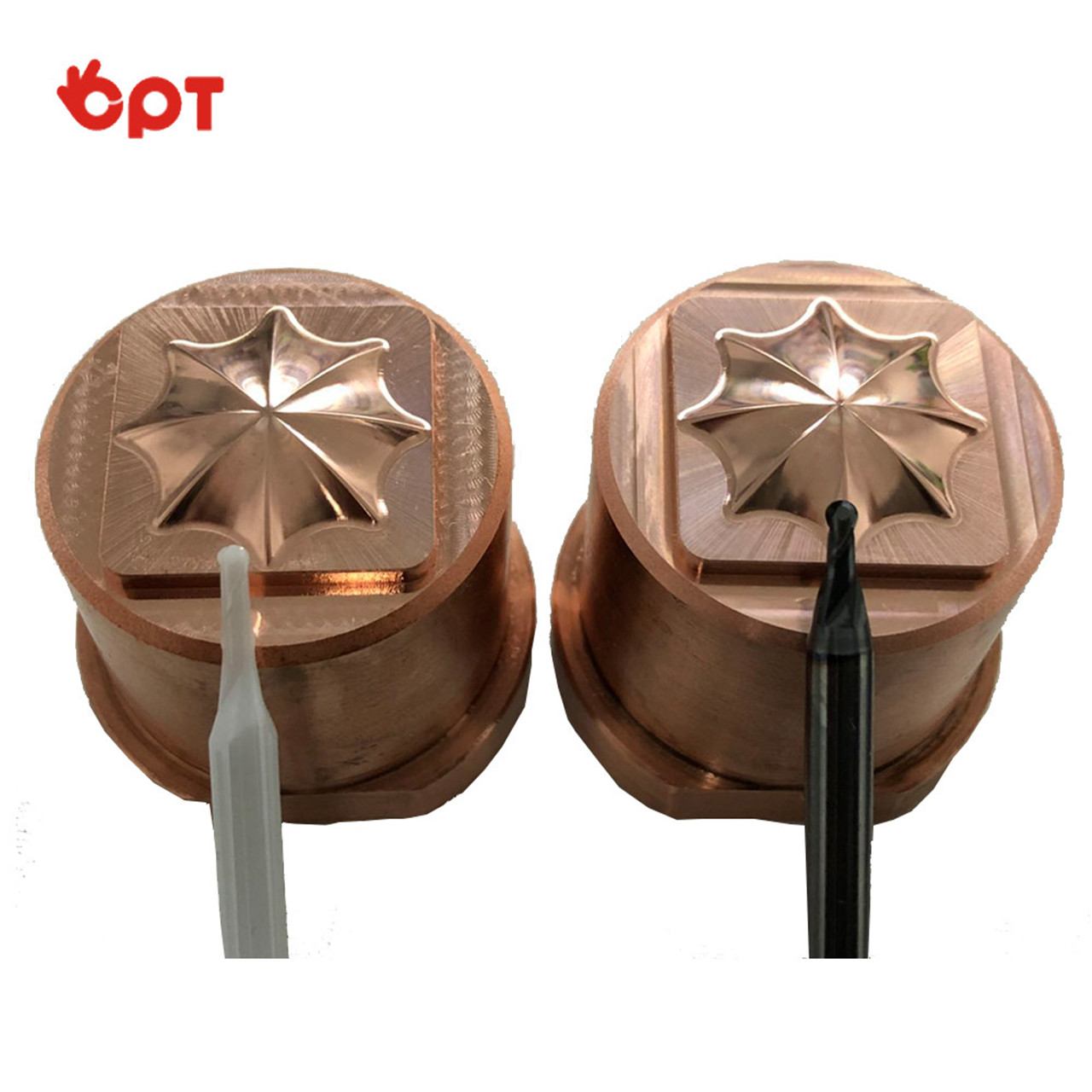
(2) Matériau céramique
Avec l’amélioration continue de sa composition, de sa structure et de son procédé de pressage, notamment le développement des nanotechnologies, les matériaux d’outils en céramique permettent de durcir les outils en céramique.Dans un avenir proche, la céramique pourrait provoquer la troisième révolution dans le domaine de la coupe après l'acier rapide et le carbure cémenté.Les outils en céramique présentent les avantages d'une dureté élevée (HRA91 ~ 95), d'une haute résistance (résistance à la flexion 750 ~ 1000 MPa), d'une bonne résistance à l'usure, d'une bonne stabilité chimique, d'une bonne résistance à l'adhérence, d'un faible coefficient de frottement et d'un prix bas.De plus, les outils en céramique ont également une dureté élevée à haute température, qui atteint HRA80 à 1200 °C.
Lors d'une coupe normale, l'outil en céramique a une très grande durabilité et sa vitesse de coupe peut être 2 à 5 fois supérieure à celle du carbure cémenté.Il est particulièrement adapté à l'usinage de matériaux de haute dureté, à la finition et à l'usinage à grande vitesse.Il peut couper divers aciers trempés et fontes trempées avec une dureté allant jusqu'à HRC65.Les céramiques à base d'alumine, les céramiques à base de nitrure de silicium, les cermets et les céramiques trempées par moustaches sont couramment utilisées.
Les outils en céramique à base d'alumine ont une dureté rouge plus élevée que le carbure cémenté.Généralement, le tranchant ne produira pas de déformation plastique dans des conditions de coupe à grande vitesse, mais sa résistance et sa ténacité sont très faibles.Afin d'améliorer sa ténacité et sa résistance aux chocs, un mélange de ZrO ou de TiC et TiN peut être ajouté.Une autre méthode consiste à ajouter des moustaches de métal pur ou de carbure de silicium.En plus d'une dureté rouge élevée, les céramiques à base de nitrure de silicium ont également une bonne ténacité.Par rapport aux céramiques à base d'alumine, son inconvénient est qu'il est facile de produire une diffusion à haute température lors de l'usinage de l'acier, ce qui aggrave l'usure des outils.Les céramiques à base de nitrure de silicium sont principalement utilisées pour le tournage et le fraisage intermittents de la fonte grise.
Le cermet est une sorte de matériau à base de carbure, dans lequel TiC est la phase dure principale (0,5-2 μm). Ils sont combinés avec des liants Co ou Ti et sont similaires aux outils en carbure cémenté, mais ils ont une faible affinité, une bonne friction et une bonne résistance à l'usure.Il peut résister à des températures de coupe plus élevées que le carbure cémenté conventionnel, mais il lui manque la résistance aux chocs du carbure cémenté, la ténacité lors de coupes lourdes et la résistance à basse vitesse et à grande avance.
(3) Nitrure de bore cubique (CBN)
Le CBN est le deuxième derrière le diamant en termes de dureté et de résistance à l'usure, et possède une excellente dureté à haute température.Par rapport à la céramique, sa résistance à la chaleur et sa stabilité chimique sont légèrement médiocres, mais sa résistance aux chocs et ses performances anti-écrasement sont meilleures.Il est largement applicable à la découpe de l'acier trempé (HRC ≥ 50), de la fonte grise perlitique, de la fonte réfrigérée et des superalliages.Par rapport aux outils en carbure cémenté, sa vitesse de coupe peut être augmentée d'un ordre de grandeur.
L'outil composite en nitrure de bore cubique polycristallin (PCBN) à haute teneur en CBN présente une dureté élevée, une bonne résistance à l'usure, une résistance élevée à la compression et une bonne ténacité aux chocs.Ses inconvénients sont une mauvaise stabilité thermique et une faible inertie chimique.Il convient à la coupe d'alliages résistants à la chaleur, de fonte et de métaux frittés à base de fer.La teneur en particules de CBN dans les outils PCBN est faible et la dureté des outils PCBN utilisant de la céramique comme liant est faible, mais elle compense la mauvaise stabilité thermique et la faible inertie chimique du premier matériau et convient à la coupe de l'acier trempé.
Lors de la coupe de fonte grise et d'acier trempé, un outil en céramique ou un outil CBN peut être sélectionné.Pour cette raison, une analyse coûts-avantages et la qualité du traitement doivent être effectuées pour déterminer lequel choisir.Lorsque la dureté de coupe est inférieure à HRC60 et qu'une faible vitesse d'avance est adoptée, l'outil en céramique est un meilleur choix.Les outils PCBN conviennent à la coupe de pièces d'une dureté supérieure à HRC60, en particulier pour l'usinage automatique et l'usinage de haute précision.De plus, la contrainte résiduelle sur la surface de la pièce après la coupe avec un outil PCBN est également relativement stable par rapport à celle avec un outil en céramique dans les mêmes conditions d'usure en dépouille.
Lors de l'utilisation de l'outil PCBN pour couper à sec de l'acier trempé, les principes suivants doivent également être suivis : sélectionner une profondeur de coupe élevée autant que possible à condition que la rigidité de la machine-outil le permette, afin que la chaleur générée dans la zone de coupe puisse se ramollir. le métal à l'avant du bord localement, ce qui peut réduire efficacement l'usure de l'outil PCBN.De plus, lors de l'utilisation d'une faible profondeur de coupe, il convient également de considérer que la mauvaise conductivité thermique de l'outil PCBN peut rendre la chaleur dans la zone de coupe trop tard pour se diffuser, et la zone de cisaillement peut également produire un effet de ramollissement évident du métal, réduire la usure du tranchant.
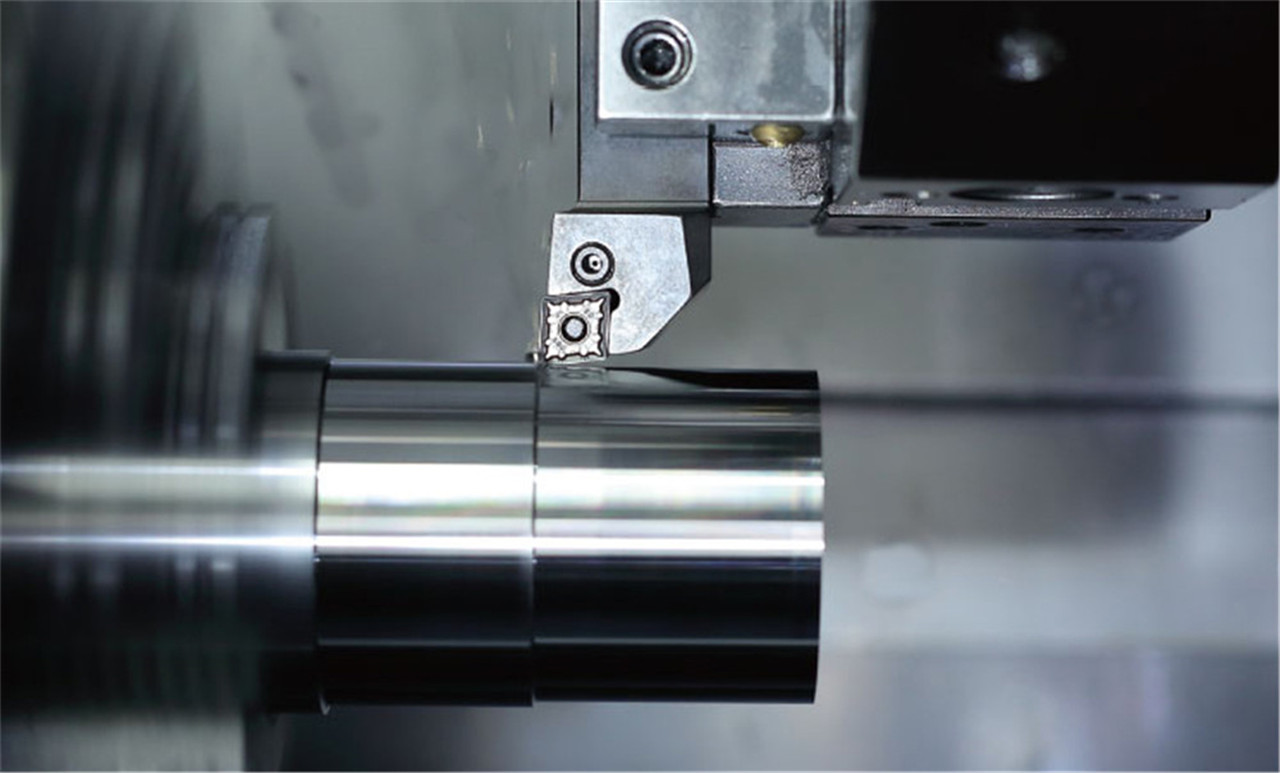
2. Structure de la lame et paramètres géométriques des outils ultra-durs
La détermination raisonnable de la forme et des paramètres géométriques de l’outil est très importante pour faire jouer pleinement les performances de coupe de l’outil.En termes de résistance de l'outil, la résistance de la pointe de l'outil de différentes formes de lame de haut en bas est : ronde, diamant 100 °, carré, diamant 80 °, triangle, diamant 55 °, diamant 35 °.Une fois le matériau de la lame sélectionné, la forme de lame présentant la résistance la plus élevée doit être sélectionnée.Les lames de tournage dur doivent également être sélectionnées aussi grandes que possible, et l'usinage grossier doit être effectué avec des lames circulaires et à grand rayon d'arc de pointe.Le rayon de l'arc de pointe est d'environ 0,8 lors de la finition μ Environ m.
Les copeaux d'acier trempé sont des rubans rouges et souples, d'une grande fragilité, faciles à casser et non contraignants.La surface de coupe en acier trempé est de haute qualité et ne produit généralement pas d'accumulation de copeaux, mais la force de coupe est importante, en particulier la force de coupe radiale est supérieure à la force de coupe principale.Par conséquent, l'outil doit utiliser un angle avant négatif (aller ≥ - 5°) et un angle arrière important (ao=10°~15°).L'angle de déviation principal dépend de la rigidité de la machine-outil, généralement de 45 ° à 60 °, afin de réduire le broutage de la pièce et de l'outil.
Heure de publication : 24 février 2023